Evaluation
This Section will focus on the Evaluation of the Prototype ViewMate. The Evaluation of the prototype gives greater insight into how the concept can be adjusted and produced into a real product. Considering the materials and improvements of the ongoing product.
Prototype
The current design features an iPad holder that holds the iPad between the female and male counterparts, held together by a spring. The distance between these is currently 25mm but should be increased to at least 50mm to make slotting on the iPad easier.
Additionally, the material of the female counterpart is not very stiff and has a low fracture point, so this should be improved. For stabilization, the piece should also feature some pins along the sliding parts to stop them from being able to move sideways.

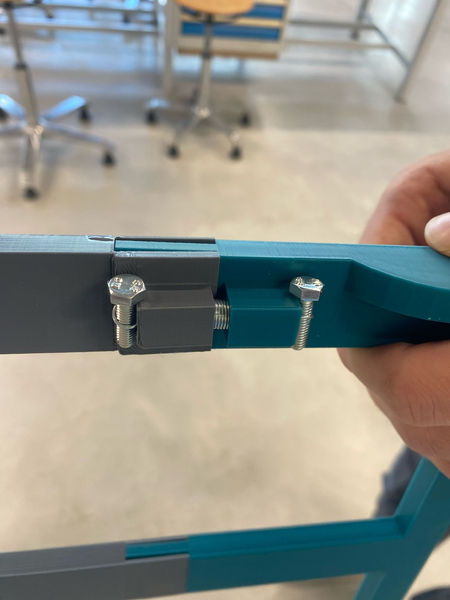
Requirements Evaluation
Although the ViewMate is ergonomically friendly for the conductor, since it was designed for him as a specific user, for the design to be released to the market or have its client base expanded, it should be adjusted to also fit the female anatomy. This is most likely not very comfortable due to the support beams going over the upper chest with the current design.
​
The usage requirement "the product can be used in multiple situations” has been met, however the transportation and storage of the product needs further development. A hinge could be used to fold up the product and a hook to hang the ViewMate up on a coat hanger could solve this.
​
The safety requirement stating that the user shall not get stuck in the product due to moving objects was not fully met. The clamp that holds the iPad in place does pose a risk of getting fingers caught, although this was decided to be left in place since the probability and severity of the possible injury is low. Other commonly used products on the market (such as a car phone holder) use the same mechanism and pose the same risk, so by standard regulations this should be fine.
​
Previously the mechanical requirement that mentions a maximum of 3 manual mechanisms was initially a maximum of 2 manual mechanisms. It was decided to change this, since the mechanisms incorporated in the product are two common mechanisms (the belt and the iPad holder), and the third, more complex one (the height adjustment) is still relatively simple since it only requires two steps (pressing in and sliding).
Materials for the Future Product
The material selection is based on the specific user's personal preference and the material's efficiency. The conductor likes an earthy style, a mixture of wood, plants, and brown color. His style was collected in a Style collage. He prefers wood, specifically timber, as a main material.
​
The iPad holder must be as light as possible for the product to be wearable for long durations. The mechanism should be durable and not break. Therefore, this part will be made from aluminum. The iPad holder will be made of Plastic and can also be 3D printed. Plastic is very light and well-suited for complex shapes. The main body of the product will be made of timber, with a soft cushion around the bottom, for a nice feeling on the shoulders. More fabric is also added for the straps around the product, to put on the iPad holder.
​
The heaviest part will be the main body, made from timber. We can estimate that these parts will be around 1L of Volume. This would lead to a weight of roughly 1kg. Combining all the elements the Product should not be heavier than 1.5kg.
The Future of the Product
After testing our prototype, we gained a clear understanding of what still needs improvement. One major issue is the weight of the main body—it needs to be lighter to ensure comfortable long-term use. A good way to achieve this is by using different materials, such as plastics.
​
The mechanism also needs refinement, particularly in terms of smooth operation and ease of use. A possible solution is to reconfigure the system using a custom-made railing, which should improve its functionality. Additionally, the iPad holder needs to be more stable. This issue could be addressed by adjusting the body, which would provide better support.
​
Constructing the product in three separate parts had several advantages. It allowed for faster assembly and gave us the ability to focus on each component individually. It also made testing more efficient, as each part could be evaluated in a variety of ways.
However, this approach also revealed a major flaw—the overall design lacks cohesion. The connections between the different parts are not well integrated, making the product feel somewhat disjointed. Moving forward, it will be crucial to refine and combine the improved parts into a final product where all components work together in perfect harmony.